Buffer polishing techniques have become a vital process in various industries, as they contribute to the overall appearance and functionality of different surfaces. These methods aim to improve the aesthetics and longevity of surfaces ranging from metal to glass, or even wood. Moreover, the proper application of polishing techniques can have a significant effect on the object’s resistance to wear, corrosion, or other damaging factors.
As a wide variety of surfaces exist, it is essential to understand that different buffer polishing techniques and materials are required to achieve optimal results. Selecting the appropriate method and tools will ensure the desired finish and reduce the risk of potential damage. Experts in the field constantly research and develop new tactics to optimize the process, addressing the unique properties and requirements of each surface type.
In order to master buffer polishing techniques, one must consider factors such as the surface composition, desired outcome, and equipment available. This article will delve into the various methods utilized for different surfaces and offer valuable insights into achieving the finest results. As the reader gains knowledge about this fascinating process, they will acquire the necessary skills to enhance the beauty and durability of multiple materials in diverse applications.
Understanding Buffer Polishing
Buffer polishing is a process used to smoothen and shine various surfaces. It employs a rotary machine equipped with a buffing pad that spins at high speeds, applying even pressure and friction to the surface. This technique can be executed on a variety of surfaces, from metal to plastic, wood to marble, and offers a multitude of benefits when performed correctly.
To achieve the desired results, it’s important to select the right buffer pad and polishing compound for the specific surface. Buffer pads are commonly made from materials such as wool, microfiber, or foam, each providing unique characteristics and finishes. Wool pads are generally more aggressive, and ideal for heavy-duty applications, while microfiber and foam pads provide a gentler approach for sensitive surfaces or delicate finishes.
Polishing compounds also play a key role in achieving a perfect finish. They contain abrasives that work in conjunction with the buffer pad to refine the surface. These abrasives come in various levels of aggressiveness, from coarse to fine grits, and influence the depth and intensity of the polishing process.
When performing buffer polishing, maintaining a consistent speed and pressure with steady, overlapping movements is crucial. Using the appropriate speed setting for the surface and pad- typically, lower speeds for sensitive surfaces, and higher for more robust materials- ensures a smooth and even finish.
Safety should always be a top priority when undertaking buffer polishing tasks. Here are a few essential tips to follow:
●Wear appropriate protective gear, such as safety glasses and gloves.
●Keep loose clothing or hair away from the machine to prevent entanglement.
●Never start the machine while the pad is in direct contact with the surface.
●Turn off the buffer and allow it to come to a complete stop before changing pads or compounds.
With proper technique and selection of materials, buffer polishing can enhance the appearance and prolong the lifespan of various surfaces. By understanding the process and practicing good safety habits, anyone can achieve professional results through this effective method.
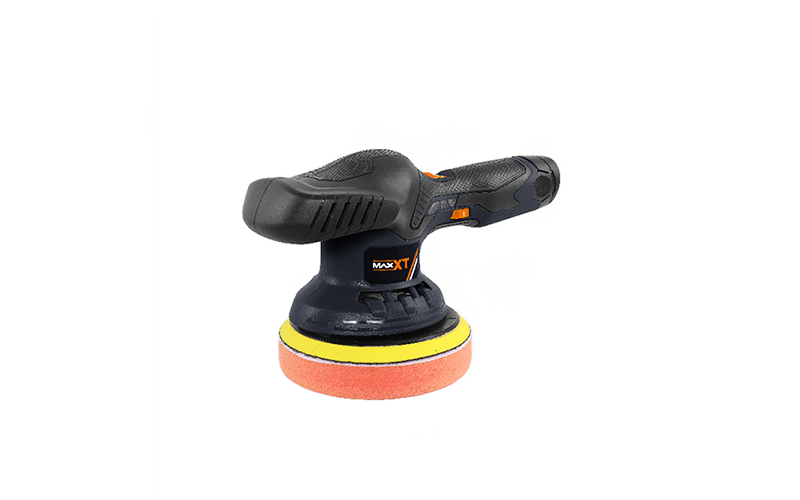
Types of Surfaces and Corresponding Techniques
Wood Surface Polishing
Wood surfaces have a natural appeal, and with proper polishing, their beauty can shine through. It’s important to understand the different types of wood surfaces, like hardwood, softwood, and veneers, before choosing a polishing technique. For best results, follow these steps:
1.Cleaning: Gently clean the wood surface with a soft cloth or vacuum cleaner to remove dirt and dust.
2.Sanding: Use sandpaper, preferably with a 120-180 grit range, to remove any imperfections and uneven surfaces.
3.Priming: Apply a layer of wood primer to ensure the polishing product bonds well with the surface.
4.Polishing: Choose a suitable polish, such as wax, oil, or varnish, and carefully apply it in thin, even coats with a clean cloth or brush.
Metal Surface Polishing
Metal surfaces also require different polishing techniques, depending on the type of metal (aluminum, stainless steel, brass, etc.). Here’s a general guide to polishing metal surfaces:
1.Preparation: Remove grime, oils, and dirt using a suitable cleaning agent and soft cloth.
2.Grinding: If necessary, use a grinding wheel or file to remove any rough edges and imperfections.
3.Sanding: Utilize wet-dry sandpaper at grits of 400, 800, and 1500 for a smooth and even finish.
4.Polishing: Select a metal-specific polishing compound, and buff the surface with a polishing wheel or cloth.
Glass Surface Polishing
To maintain the clarity and smoothness of glass surfaces, take special care while polishing. These steps will help you achieve a streak-free, flawless finish:
1.Cleaning: Start by cleaning the glass with a glass cleaner or water-vinegar solution, and remove any debris with a soft cloth or squeegee.
2.Inspection: Check for scratches or imperfections that could affect the polished finish.
3.Sanding: If necessary, use specialized glass-polishing discs or sandpaper with a grit of 2000 or higher to remove scratches.
4.Polishing: Apply a high-quality glass polish with a clean microfiber cloth or specialized glass-polishing pad, buffing in a circular motion for the best results.
Choosing the Right Polishing Equipment
When it comes to buffer polishing techniques, the equipment you choose plays a significant role in achieving the desired results. In this section, we’ll discuss how to select the right polishing equipment for different surfaces.
First, consider the surface material. Different materials require specific types of polishing tools to ensure proper polishing without damaging the surface. For instance, metal surfaces need buffing wheels made from materials like sisal, cotton, or wool. On the other hand, plastic and wood surfaces often require cloth or foam pads.
Size and shape of the surface also matter when selecting polishing equipment. For tight spaces and intricate details, smaller polishing tips or cones are ideal. In contrast, larger buffing wheels or pads work well on broad surface areas. Choose a tool that matches the size and contours of the surface you’ll be working on.
Next, pay attention to the type of polishing compound. There are countless polishing compounds available, each with unique abrasive properties and ingredients deemed suitable for specific surfaces. To ensure optimal results and prevent damage, use a compound that’s designed for the material you’re polishing.
Adjustable speed in polishing tools is another essential factor not to be overlooked. Different surfaces and polishing compounds require varying speeds to achieve a flawless finish. Investing in a tool with adjustable speed settings allows you to work on multiple surfaces and materials confidently.
Lastly, consider the ergonomics and safety of your chosen equipment. A device that’s comfortable to hold and maneuver will reduce fatigue and increase precision during prolonged use. Also, ensure that your polishing tool has safety features like a well-fitted guard or shield to protect you from flying debris.
In summary, choosing the right polishing equipment involves assessing the surface material, size, and shape, as well as selecting the appropriate polishing compound. Additionally, look for tools with adjustable speed settings, ergonomic design, and safety features to ensure a successful polishing experience.
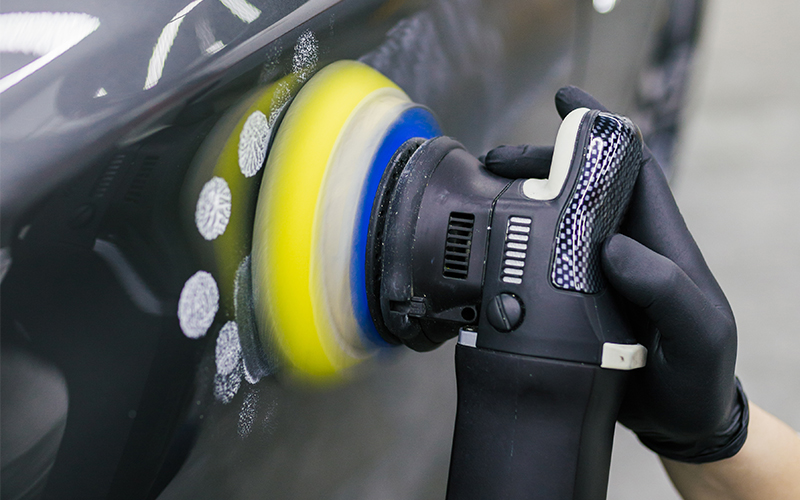
Common Mistakes and Their Prevention
When it comes to buffer polishing techniques for different surfaces, it is crucial to be aware of common mistakes and how to prevent them. This will ensure a smooth and efficient polishing process, resulting in a high-quality finish.
One common mistake is using the incorrect polishing compound for the surface material. This can result in poor performance and even damage to the surface. To prevent this, always research and use the appropriate compound for the specific surface you are working on. This may include referring to the manufacturer’s instructions or consulting experts in the field.
Another common mistake is selecting the wrong buffing pad or wheel. There are various types of pads and wheels designed for specific applications. Using the wrong type can lead to inadequate results or damage to the surface. To avoid this, ensure you are using the correct pad or wheel for the intended application and replacing them when they are worn out.
It’s also crucial to maintain the appropriate speed and pressure during the polishing process. Applying too much pressure or using excessively high speeds can cause damage to the surface and potentially result in an uneven finish. Always consult the manufacturer’s guidelines for the recommended speed and pressure settings for your equipment and workpiece.
In addition, not properly cleaning and preparing the surface before the polishing process can lead to inadequate results or even cause damage. Ensure the surface is free from dirt, dust, and oils before starting the process. You can use a cleaning solution and a cloth to remove any contaminants.
Finally, a lack of routine maintenance on your polishing equipment can lead to poor performance and affect the quality of your work. Regularly inspect your equipment, clean and lubricate moving parts, and replace worn-out components to keep your tools in optimal condition.
By being aware of these common mistakes and implementing preventative measures, you can improve the efficiency and quality of your buffer polishing process, resulting in more appealing and longer-lasting finishes on various surfaces.